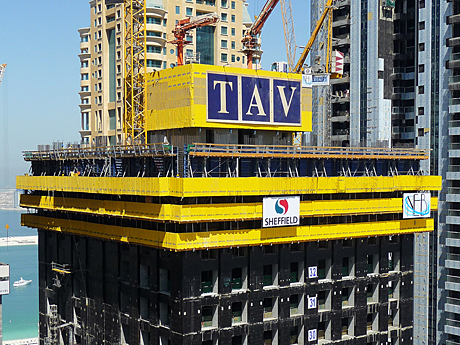 The central core and the columned facade of the 425 m high Marina 101 are being built in record time with automatic climbing formwork from Doka. Platform SCP is being used on the core to keep the cycle times extremely short and maximise workplace safety. Doka’s high-end SKE 50 automatic climbers and folding formwork are the systems in use for the facade. |
 Marina 101 is a new and superlative skyscraper now under construction in the immediate vicinity of the Palm Jumeirah and the exclusive Dubai Marina megaproject. One hundred and one floors and a soaring 425 metres tall, Marina 101 joins the exclusive set of supertall towers, those iconic high-rise buildings more than one hundred floors high. At this time Dubai counts “only” five supertowers ranking in this category. The central CIP core and the imposing columned facade of Marina 101 are being built in record time with automatic climbing formwork from Doka. Platform SCP is being used on the CIP core to keep the cycle times extremely short and maximise the level of industrial safety on the build. Doka’s high-end SKE 50 automatic climbers and folding formwork are the systems in use for the facade. |  |
Completion is scheduled for 2011 and the first 28 floors of Marina 101 will house a luxury hotel with 324 superlative suites. There will be 505 exclusive apartments on floors 36 and above. Speedy progress, in other words short cycle times for cast-in-place concreting, was a top priority for lead contractor TAV Construction and the crunch factor in the decision to contract Doka as the formwork partner. Platform SCP is fine-tuned for maximum efficiency, the site crew is totally familiar with the routine, and it all adds up to a four-day cycle for each complete floor – impressive performance by any standards. The number of concreting sections is high of 110, so time savings on the carcass work are tremendous. Platform SCP makes for fast builds, but it also has another crucial benefit to offer. The platform leads the floor-slab formwork by only two floors, so the free headroom can be utilised to maximum benefit to keep the work zone of the overhead crane clear and unobstructed. “That is a crunch factor for us and it helps us keep to the very ambitious schedule on this build. We have fewer climbs for the crane and that makes for a huge saving on time”, emphasizes Volkan Yerdelen, TAV’s Construction Manager on the Marina 101 build. |  |
Platform SCP climbs on 8 extremely powerful hydraulic cylinders; total available load-bearing capability in the climbing and working phases alike is in excess of 45 metric tons. In addition, the platform climbs the formwork for all 6 shafts plus a suspended stairwell tower for safe and speedy access to the working levels, along with two high-capacity concrete pump distributors. A note in passing: Per lifting unit and concreting section, the platform SCP design calls for only two box recesses to locate the supporting beams in the concrete structure. Other platform solutions, by contrast, need twice as many box recesses (all of which have to be locked into the reinforcing structure) and a significantly higher number of rams for climbing. To maximise flexibility in the concreting process for the building core, the columns and the floor slabs, the concrete pump distributors are climbed with the platform’s climbing mechanism but independently of the core formwork. “We can climb the formwork and the concrete pump distributors separately, so there are virtually no mandatory-position points when we concrete. That gives us maximum versatility and, even more importantly, highly efficient material utilisation”, asserts Siva Shankar Kanagasabai, Project Manager with TAV. On this project, too, climbing the platform SCP for the CIP core and the SKE 50 brackets for the external wall sections separately proved the right strategy for efficient and perfectly harmonised formwork deployment right from the word go. The six sublevel floors and the multi-level podium that is a signature feature of this project called for extensive CIP concreting, but even so the platform could be climbed independently so as to optimise material utilisation. |  |
The two working levels of the platform SCP are fully enclosed for maximum safety and protection against the weather. The platform is permanently anchored in the finished concrete so lifts are possible even in windy conditions and construction can proceed rapidly and without unexpected hitches. The central building core has no less than six shafts and is being formed with 815 m² of Doka Top 50 beam formwork. The number of cycles is high – remember there are 115 concreting sections to be formed on this build – so the beam formwork is skinned with extremely durable Dokaplex sheets. Steel formwork is being used at the corners to enhance durability even further. Each anchor hole has extra protection, because here again a high number of re-use cycles is of tremendous benefit in terms of speed. These reinforcements proved more than worthwhile on the Burj Dubai build and enable the 400-plus metres of the supertower’s soaring CIP core to be climbed with only one change of formwork sheeting. | 
|
The 32 columns in the building’s iconic facade are being cast with Doka’s high-end SKE 50 automatic climbing formwork. One each side of the building the climbing brackets are joined together to form a set so that they can all be climbed at the same time at the touch of a button. The facade formwork has folding side panels for fast forming and stripping out times. The rear of each of the massively proportioned columns is being formed with hand-set Doka Frami framed formwork. The forming crew from ATC strips out the Frami sections and simply places them on the two main working platforms of the SKE 50 automatic climbers, ready for the climb to the next concreting section. The routine is practical and efficient, and it enables the column formwork and the formwork for the sides of the bottom joists to be moved up from level to level without any craneage whatsoever. The site crew from TAV Construction is using manual-set formwork for the massive CIP bottom joists at the edges of the floor slabs. A mere 12 hours after the concrete is poured, the edge shuttering can be stripped out independently of the bottom-joist side formwork so that the crew can press ahead with the lead-in work. That ensures compliance with the tight schedule in every phase of the work cycle and speedy progress on the build. |
|
 From DOKA News 12/Nov/2009 |
|
|
|
Quick Link
|
|
|
|