
High-performing Doka automatic climbing formwork SKE 50 was used to form four towers at a cement plant in southern Italy, in record time. |
|  |
|
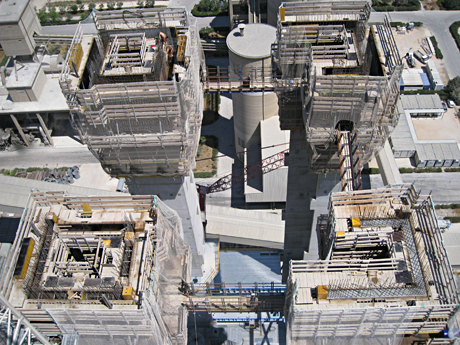 |
With an annual production volume of 72 million tonnes and more than 60 cement plants in 22 countries, the Italcementi Group is the world’s fifth-largest producer of cement. To boost the productivity of its plants at the same time as cutting pollutant emissions, this cement giant is continually investing in the modernisation of its production locations. A recent example of this is the Italcementi cement plant at Matera in southern Italy. The centrepiece of the extensive modernisation measures undertaken here was the installation of a vertically oriented rotary kiln for producing cement clinker. The supporting construction for the large-volume cylinder of this rotating kiln is provided by a combination of four 90 m tall CIP concrete towers and a massive steel framework. Doka automatic climbing formwork SKE 50 was fielded on this construction project to ensure fast, cost-effective construction progress.
Efficient formwork solution for a rapid construction progress
Two of these towers also serve to provide operator access to the new production plant and so have been built with a rectangular layout and a stairwell shaft. The opposite towers have a load-bearing function only, and are thus designed as solid wall piers with a C-shaped cross-section. In the light of its positive experience on a similar project, main contractor Si.Ste.Ma Costruzioni opted for a self-climbing formwork solution from Doka. 48 high-performing Doka SKE 50 automatic climbers and 680 m² of Doka large-area formwork Top 50 were in action here to cast these four towers, each of which was divided into 20 casting steps. Using this Doka equipment, more than 3400 m³ of self-compacting concrete was formed the “Safe. Fast. Efficient.” way. The site crew working under foreman Giancarlo Pellegrini had already had experience of how to assemble and use the automatic climbing formwork correctly, and this – plus the assistance given them by an experienced Doka field service technician at the beginning of the forming operations – let them achieve a record-breaking three-day cycle for the 4.5 m high casting steps. In some cases, they even managed to finish two casting sections in just five days. “In terms of both safety and handling, the SKE 50 automatic climbing formwork system has got me convinced. Thanks to its powerful hydraulic cylinders, it only took us just a few minutes to climb the large formwork gangs up to the next casting section, absolutely safely, after which we were able to start setting up the formwork again straight away. What’s more, the generously sized working platforms gave us plenty of handling space for stripping and cleaning the gangs”, says foreman Giancarlo Pellegrini, neatly summing up the benefits of the high-performing Doka automatic climbing formwork.
Ingenious work-cycle for rapid construction progress
Much of the credit for this fast construction progress is due to the workflow plan devised by the experienced project technicians of Doka Italia, which ensured that work could move ahead swiftly and economically in every phase of the forming operations. In order to obtain optimally co-ordinated working cycles, the four towers were divided into two independent climbing cycles. The two towers of the first casting section were climbed in parallel with one another, as were the towers of the second casting section. However, the former were cast one section in advance of the latter. “By cycling the operations in this way, we were able to optimally co-ordinate the forming and reinforcement work and to accelerate overall construction progress”, points out foreman Giancarlo Pellegrini. To enable the site crew to move back and forward between the workplaces here as quickly and efficiently as possible, the four towers were linked together by catwalks. Thanks to this ingenious solution, only one building-site hoist was needed to provide access to the towers. These catwalks were originally developed by Doka for automatic climbing assignments on bridge pylons, and are directly connected to the main working platforms on the self-climbing scaffolds. The height difference between the two towers being cast in advance and the pair of towers following one casting section behind was bridged by a vertically moveable catwalk. “By using these catwalks, we had permanent access links between the automatic climbing formwork units on the four towers at all times, throughout the entire shell construction phase. This was a huge advantage – especially when you consider that the towers were 90 m high. The alternative would have been four building-site hoists, but economically this is just not viable”, points out Giancarlo Pellegrini, underlining the added value of this solution in terms of easing the pressure on the site logistics.
With its detailed planning of the forming operations, the professional support given to the site crew by an experienced Doka field service technician during construction start-up, and the ongoing assistance it provided throughout the whole shell construction phase, Doka Italia made a major contribution towards executing this project in-time and on-budget, meeting all requirements to the client’s complete satisfaction.
|
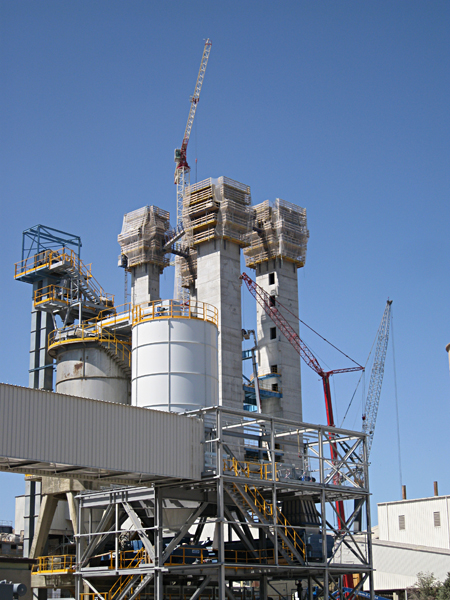 |
 From DOKA News 14/Aug/2009 |
|
|
|
Quick Link
|
|
|